Biznes Fakty
AI rozpycha się w poznańskiej fabryce Unilever. „Zużywamy aż 5 tys. ton wody mniej” [WYWIAD]
Monika Budna, digital and manufacturing excellence manager w Unilever, wyjaśnia, w jaki sposób sztuczna inteligencja poprawia efektywność poznańskiej fabryki. Poznajemy też podejście Unilever w kontekście ryzyka zastępowania pracowników rozwiązaniami AI i automatyzacją. — Wraz z rozwojem technologicznym fabryki nie maleje liczba miejsc pracy, a zmieniają się wyzwania, rola człowieka i charakter wykonywanej przez niego pracy — tłumaczy nasza rozmówczyni.
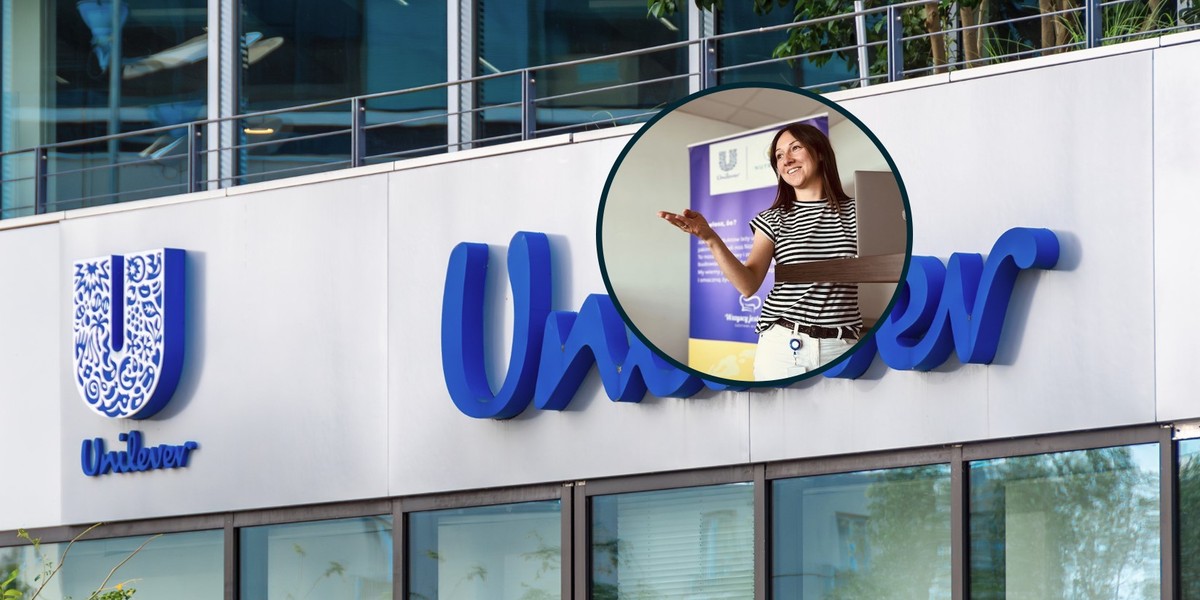
- Unilever w poznańskiej fabryce wykorzystuje sztuczną inteligencję m.in. do optymalizacji zużycia wody i środków czyszczących podczas mycia linii produkcyjnych
- AI i automatyzacja pomagają zapobiegać błędom w pakowaniu produktów
- W ramach programu AI for Safety Unilever monitoruje ponadto potencjalnie niebezpieczne sytuacje w fabryce, zapewniając pracownikom bezpieczeństwo przy jednoczesnym zachowaniu ich pełnej anonimowości
- „Zapewniamy też rozwój zawodowy poprzez cyfrowy upskilling i szkolenia dostosowane do nowych wymagań technologicznych”
- Więcej informacji o biznesie znajdziesz na stronie Businessinsider.com.pl
Grzegorz Kubera, Business Insider Polska: Macie państwo fabrykę w Poznaniu, w której stosowana jest sztuczna inteligencja. Unilever w tej fabryce wytwarza głównie żywność, np. marek Knorr czy Amino. Do czego wykorzystywana jest zatem AI?
Monika Budna, digital and manufacturing excellence manager w Unilever: Pierwsze wdrożenie AI w fabryce dotyczyło analizowania danych i odbyło się już ponad 2 lata temu. Obecnie sztuczną inteligencję wykorzystujemy już do wielu obszarów, a pierwszym, o jakim mogę wspomnieć, jest stosowanie algorytmów AI do optymalizacji zużycia wody.
To znaczy?
Jako fabryka, która produkuje żywność i to w głównej mierze żywność mokrą, czyli zupy, sosy czy majonez, zużywamy spore ilości wody. Po procesie produkcyjnym linie należy oczywiście umyć, co dzieje się w sposób automatyczny, jednak zawsze można dany proces usprawnić. Przez specyfikę naszej produkcji nie możemy wyeliminować używania wody, ale możemy zrobić bardzo dużo, aby zużywać jej jak najmniej, co jest korzystne zarówno dla finansów spółki, jak i środowiska.
Doszliśmy do wniosku, że najnowsze rozwiązania technologiczne mogą nam w tym pomóc i zoptymalizować mycie naszych linii produkcyjnych. Zależało nam, aby zredukować zużycie wody, ale też środków czyszczących, jak również skrócić sam proces mycia. Wdrożyliśmy więc spektrofotometry i odpowiednie oprogramowanie oparte na AI i machine learningu. Środki myjące wykorzystywane w procesie mycia przepływają przez szereg czujników, a AI podpowiada — na podstawie już zdobytej wiedzy — czy można zakończyć proces mycia, bo linia produkcyjna jest już czysta. Nauczyliśmy AI, jak określać poziom czystości i przeprowadziliśmy wiele testów i analiz, uwzględniając ogrom danych. Duża część tej pracy jest obecnie zautomatyzowana i zoptymalizowana.
Dziś AI analizuje wszystkie dane w czasie rzeczywistym i w każdym cyklu mycia decyduje o tym, kiedy dany obiekt jest już czysty.
Czy wdrożenie takiego rozwiązania to opłacalna inwestycja, czy raczej trzeba poczekać kilka lat, zanim wypracowane oszczędności wypracują zwrot?
Sam system nie był bardzo kosztowny. Biorąc pod uwagę ilości mediów, jakie oszczędzamy w skali roku, udało nam się skrócić jeden cykl mycia o prawie godzinę. Projekt optymalizacji procesu mycia został wdrożony jako pilotaż — na razie AI odpowiada za cykl mycia na jednej linii produkcyjnej i widzimy wiele korzyści płynących z zastosowania tego rozwiązania.
Jednocześnie ma to duży wymiar środowiskowy, bo zużywamy aż 5 tys. ton wody mniej, czyli tyle, ile mieści się w dwóch pełnych basenach olimpijskich. Dla nas ten aspekt środowiskowy jest bardzo ważny. Nie tylko więc uwalniamy w każdym cyklu godzinę pod efektywną produkcję i redukujemy koszty, ale też zużywamy znacznie mniej wody. Jeśli więc chodzi o bilans zysków i strat, nie ma tu nawet o czym dyskutować — to po prostu ma sens. Będziemy rozszerzać te działania na kolejne linie produkcyjne.
Czy AI stosowana jest jeszcze do innych zadań w poznańskiej fabryce Unilever?
Tak, mamy np. system, który zapobiega ewentualnemu wprowadzeniu na rynek produktu ze źle dobranymi składnikami. Chodzi tutaj o tzw. cross-packing. Wyobraźmy sobie opakowanie, w którym znajdują się różne komponenty, każdy w osobnej saszetce, takie jak warzywa, przyprawy czy orzechy. Klient może kupić taki produkt i przygotować z niego w domu posiłek w krótkim czasie. Dla nas z kolei to jest dość trudny produkt do przygotowania, ponieważ do opakowań musimy włożyć odpowiednie ilości właściwych komponentów — są to różne składniki, często dość podobne do siebie.
Udało nam się z pomocą automatyzacji i AI stworzyć taki proces, w którym saszetki ze składnikami są podczas produkcji umieszczane w opakowaniu jednostkowym, a system kamer samodzielnie sprawdza, czy umieszczono w nim odpowiednie komponenty. W przypadku wykrycia niezgodności opakowanie jest automatycznie odrzucane z linii pakującej.
To oczywiście przydatne, ale wydaje się, że podobne rozwiązania działają na rynku od lat.
Tak, niemniej warto podkreślić, że nasz system nadzoruje nie tylko proces samego pakowania, ale zapobiega także pomyłkom. Przykładowo jest w stanie wykryć, za pomocą technologii deep learning, brak konkretnego komponentu albo błędne dodanie innego składnika — np. przez błąd ludzki. Mamy więc system kamer wykorzystujący autorskie algorytmy, który rozpoznaje poszczególne elementy na linii produkcyjnej – najpierw po kształcie, a następnie również po tym, co jest napisane na saszetkach i definiuje, czy to na pewno odpowiedni komponent do danego produktu.
Czy takie błędy zdarzają się często?
Nie, na szczęście tego typu pomyłki zdarzają się bardzo rzadko, natomiast i tak robimy wszystko, aby im zapobiegać i traktujemy to niezwykle poważnie. Wyobraźmy sobie, że zamiast suszonych warzyw w opakowaniu – na którym widnieje informacja, że produkt nie zawiera orzechów – znalazłyby się jednak orzeszki. Gdyby produkt kupiła osoba, która jest uczulona na orzechy, byłoby to realne zagrożenie dla jej zdrowia, a nawet życia. W Unilever bezpieczeństwo konsumentów to fundament naszej działalności, a więc tego typu sytuacje są niedopuszczalne. Dlatego zainstalowaliśmy właśnie taki system wizyjny z deep learningiem, który wspiera nas w dostarczaniu najwyższej jakości, bezpiecznych produktów. To tym bardziej przydatne rozwiązanie, bo komponenty w tych konkretnych produktach znajdują się często w przezroczystych saszetkach i nie ma możliwości nadruku na nich kodów, albo sam dostawca zapewnia właśnie takie saszetki i też nie jesteśmy w stanie ingerować w to, jak są przygotowywane. Z pomocą AI mamy pewność, że właściwe komponenty trafiają do właściwych produktów.
Czy wcześniej takimi zadaniami zajmował się pracownik?
Tak, pracownik ręcznie wkładał komponenty do pudełek, a kontrola jakości odbywała się zgodnie z ustalonym reżimem. Teraz, dzięki temu rozwiązaniu, mamy pewność, że 100 proc. produkcji jest zgodne z wymogami.
Czytaj też: Sztuczna inteligencja nie zwalnia z myślenia. Młodzi używają jej coraz częściej — nierzadko w niewłaściwy sposób
Monotonne zadania przejmują automaty. Pracownicy zyskują szkolenia
Czy osoby, które wcześniej zajmowały się zadaniami, jakie zostały zautomatyzowane i oddane w „ręce” sztucznej inteligencji, wykonują teraz inne czynności?
Automatyzacja i AI uwalniają czas naszych pracowników do wykonywania bardziej wymagających prac, gdzie mogą wykorzystywać szersze umiejętności.
Jeśli natomiast pracownik, który realizował zadania związane z pakowaniem produktów, oddaje je teraz automatyzacji, to czy jest zwalniany?
Sztuczna inteligencja budzi wiele obaw, zwłaszcza że rozwiązania do automatyzacji są już tak skuteczne i precyzyjne. To jednak nie oznacza, że zastępujemy pracowników narzędziami AI.
Prowadzimy bardzo szeroko zakrojone procesy szkoleń dla wszystkich szczebli stanowisk, które mamy w fabryce — od operatora linii produkcyjnej po specjalistów technicznych i inżynierów. Wraz z rozwojem technologicznym fabryki nie maleje liczba miejsc pracy, a zmieniają się wyzwania, rola człowieka i charakter wykonywanej przez niego pracy.
Na czym polegają te szkolenia?
Wraz z rozwojem fabryki pojawiają się nowe wyzwania związane z poprawą efektywności i bezpieczeństwa naszej pracy. Szkolenia dotyczą więc obsługi naszych systemów produkcyjnych, aplikacji, analizy danych oraz oczywiście nowoczesnych maszyn i technologii.
Jest to więc podwyższanie kompetencji zawodowych, aby dostosować je do zmieniających się wymagań rynku pracy? Krótko mówiąc: upskilling?
Zdecydowanie tak. To cyfrowy upskiling, który realizujemy w formie odrębnych akademii dla trzech grup naszych pracowników. Prowadzimy szkolenia dla operatorów maszyn, pracowników działu technicznego oraz inżynierów wspierających procesy produkcji. Dużą część szkoleń realizujemy dzięki wsparciu naszych ekspertów wewnętrznych, ale chętnie również pozyskujemy wiedzę od naszych stałych partnerów i dostawców. Uspkilling jest wpisany w naszą długoterminową strategię rozwoju, którą nazywamy w Unilever Future of Work.
Warto pochwalić takie praktyki. Zwłaszcza że w ostatnich miesiącach często słyszy się, że firmy raczej zwalniają personel i zastępują wiele zadań automatami i AI. Zapytam jednak, czy pracownicy chętnie pozyskują takie umiejętności? Zakładam, że jeśli ktoś pracował przy linii produkcyjnej, a teraz ma nagle uczyć się obsługi jakiegoś oprogramowania IT, może mieć problem z opanowaniem nowych umiejętności.
Zdarzają się osoby, które podchodzą do takich szkoleń i poszerzania kompetencji z rezerwą, ale tłumaczymy wówczas, że są to kompetencje niezbędne po prostu do funkcjonowania w dzisiejszym świecie, więc poprawią jakość życia pracownikom także poza pracą.
Sprawdź też: Jeden, by wszystkimi rządzić. Amazon zaskoczył możliwościami AI
Monitoring z AI a ochrona prywatności
Wiem też, że Unilever wykorzystuje w Poznaniu system monitoringu z użyciem AI. Do czego służy i co konkretnie rejestrują kamery?
To działanie w ramach programu AI for Safety, czyli sztuczna inteligencja dla bezpieczeństwa. W tym kontekście chodzi o bezpieczeństwo naszych pracowników. Zawsze powtarzamy, aby poszczególne osoby wykonywały swoje obowiązki w uważny sposób, zwracając uwagę na to, co znajduje się dookoła i jakie zadania wykonują maszyny. Mamy też zasadę: jeśli widzisz, że coś nie działa poprawnie i może zagrażać bezpieczeństwu, odejdź ze stanowiska pracy i zgłoś to odpowiednim specjalistom.
Poproszę o podanie przykładu.
Jedną z zasad, jaką wyznajemy, jest to, żeby trzymać się poręczy podczas poruszania się po klatkach schodowych. Niby prosta rzecz, ale jednak może uratować komuś zdrowie. Nie możemy być wszędzie i widzieć wszystkiego, więc prosimy pracowników o przestrzeganie konkretnych zasad, by unikać potencjalnie niebezpiecznych sytuacji i wypadków.
Mamy kilka takich miejsc, bardzo newralgicznych i potencjalnie niebezpiecznych, gdzie krzyżują się np. drogi piesze z drogami transportowymi dla wózków widłowych, są tam również podesty, na które prowadzą schody. Wprowadziliśmy więc system monitoringu z AI, który jest w stanie rozpoznawać i zapisywać niebezpieczne sytuacje – na przykład, kiedy ktoś schodzi czy wchodzi po schodach, nie trzymając się poręczy. Odpowiednie oprogramowanie w czasie rzeczywistym analizuje wszystko to, co dzieje się w danym obszarze i potem wiemy, do jakich sytuacji dochodzi i co musimy poprawić.
A co z prywatnością? Może ktoś nie chciałby być nagrywany przez kamery?
Oczywiście wzięliśmy pod uwagę prywatność. Wykorzystywane przez nas oprogramowanie wykorzystuje trwały filtr nakładany na obraz, który zapewnia pełną anonimowość naszych pracowników — ich twarze są zamazane. Zresztą, wdrażane przez nas procedury i systemy wykorzystujące AI w zakresie bezpieczeństwa mają na celu podnoszenie standardów, a nie karanie pracowników. Stawiamy na edukację i podnoszenie świadomości pracowników w obszarze potencjalnych zagrożeń oraz rozwijanie kultury uważności – na bezpieczeństwo siebie i innych. A tego typu rozwiązania bardzo nam w tym pomagają.
Czy nagrania z kamer są później do czegoś wykorzystywane?
Przede wszystkim do budowania kultury bezpieczeństwa w fabryce. Jeśli w jakimś miejscu często dochodzi do łamania zasad bezpieczeństwa i system to zarejestruje, możemy później przeprowadzić spotkanie z pracownikami z konkretnego zespołu i pokazać na wideo, co warto poprawić dla zwiększenia bezpieczeństwa. Uczestnicy spotkania widzą wtedy na naszym, konkretnym przykładzie, a nie z materiału znalezionego w sieci, co było niebezpieczne, co może potencjalnie skończyć się źle. Zyskują ceny feedback na temat tego, co warto poprawić i dlaczego. Takie działania skutecznie uwrażliwiają pracowników na odpowiednie praktyki.
W przyszłości planujecie Państwo więcej wdrożeń AI?
Mamy wiele projektów, które już w mniejszym czy większym stopniu zasilane są AI. Można powiedzieć, że to wszystko rozpędza się niczym kula śniegowa. Przetarliśmy szlaki i widzimy, jak duże korzyści przynosi wdrażanie nowoczesnych technologii. Projekty pilotażowe zostaną teraz wdrożone na możliwie największej liczbie linii produkcyjnych. Ciągle też jesteśmy na etapie analizowania, gdzie jeszcze AI może nam pomóc oraz jak w inny sposób zoptymalizować daną operację.
— Rozmawiał Grzegorz Kubera
Monika Budna — liderka programu digitalizacji w poznańskiej fabryce Unilever, wieloletnia kierowniczka ds. R&D/T&I, aktualnie kierowniczka działu digitalizacji i efektywności produkcyjnej. Ma doświadczenie w zakresie technologii przetwarzania żywności, produktów mokrych, suchych i aromatów. Budowała je głównie, przez ponad 13 lat, w Unilever Polska.
Dziękujemy, że przeczytałaś/eś nasz artykuł do końca. Bądź na bieżąco! Obserwuj nas w Wiadomościach Google.
Źródło